3 proven methods for restoring your last-stage steam turbine blades to as good as new
- Date
- November 29, 2022
- Category
- Views
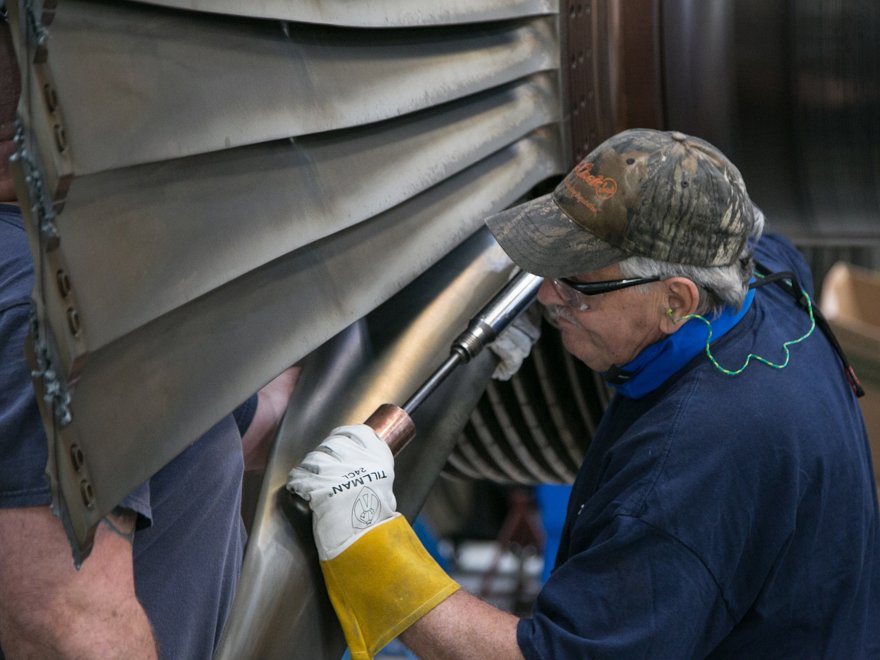
How to save on costs and extend the life of your last-stage steam turbine blades
Replacing last-stage blades in the low-pressure section of a steam turbine can be prohibitively expensive. It also tends to be accompanied by long lead times – especially with the challenging supply chain issues we’re seeing more and more today.
So what if you could make cost savings of as much as 60% and reduce your outage time frame without losing efficiency or sacrificing blade integrity?
That was the subject of a webinar we recently gave in partnership with Combined Cycle Journal.
Ian Saeger, Manager of Project Engineering at EthosEnergy, shared the proven methods our steam turbine engineering team has developed to repair these critical blades at a fraction of the cost of replacing them – at the same time reducing your carbon footprint by extending the life of your steam turbine blades.
By talking through three case studies, Ian introduced the webinar attendees to a number of our in-situ blade repair solutions.
Here, you can read a snapshot of Ian’s presentation and get an insight into what our steam turbine blade repair methods can do for your critical assets.
But first…
What are the main causes of damage to steam turbine blades?
There are three leading causes of repairable damage to last-stage steam turbine blades.
1. Water droplet erosion
This is the number one cause of damage. Indeed, a poll taken at the beginning of our webinar found water droplet erosion to have been the main reason behind replacing last-stage steam turbine blades for 70% of the attendees.
It can lead to cracking in the airfoil. And with enough material removal, the natural frequencies of the blades can shift into resonance. This can rapidly cause high-cycle fatigue failure.
2. Cover or tenon cracking
Often the result of improper peening at assembly, microcracks develop and grow over time. They can eventually lead to failure of the tenon or cover.
3. Foreign object damage (FOD)
When we talk about large steam turbine blades, we’re generally referring to L-0 or L-1 blades. Any failure of an upstream component that results in the liberation of material will almost always cause damage to downstream blades.
Our in-situ blade repair solutions in action
Water droplet erosion repair
The first case study Ian discussed is a good example of how we carry out an in-situ repair of water droplet erosion damage.
Our client asked us to inspect a couple of large dual-flow rotors that had been in storage. We found severe leading-edge erosion to the L-0 and L-1 blades. Our concern was that the outer lacing wire was right in the middle of the eroded area on the L-0 blades. If left unrepaired, this would have posed a risk of a crack propagating in the lacing-wire hole.
We removed the outer lacing wire, which gave access for the blade repair without having to remove any blades. Initially, we repaired four blades to a finished condition. This allowed us to make sure there were no issues at any stage of the repair.
Our strategy then was to carry out a weld overlay repair to every other blade. This minimized the risk of distortion to the inner lacing wire left in place. We also restored the airfoil to its original geometry but with the inclusion of Stellite leading-edge protection, extending the life of the blades.
Keeping an outage on schedule with a cover cracking repair
Our second example involved a repair of a crack in the last-stage of a blade for a GE D11 turbine.
During a major outage inspection, we discovered a crack on the L-0 blade tip of the LP rotor measuring just 3/8ths of an inch. The problem for our client was that replacing the entire row of blades would have been hugely expensive – costing in the region of $2 million – and it would have inevitably involved lengthy lead times.
Our engineering team determined that the blades could be repaired in situ. One of our specialist welders from our center of excellence for steam turbine blade repairs in Worcester, UK, came over and carried out a weld repair.
This gave our client significant cost savings and avoided further damage from the crack propagating.
Had the crack not been discovered, this could eventually have led to catastrophic failure of the blade, necessitating a lengthy outage. Instead, we managed to keep the client’s planned major outage on schedule.
Severe foreign object damage repair
Our final example concerned a pretty serious case of foreign object damage.
An upstream failure of some of the blades in the preceding L-1 stage was passed through to the L-0 stage, causing these large freestanding blades to suffer severe damage. The OEM recommended the blades be replaced.
But when our blade repair specialists evaluated the damage, they determined it would be possible to restore the blades by performing a full tip repair. Although absent from the original design of the blades, our solution included adding leading-edge erosion protection to help prolong the life of the blades.
As with our first example, this was a two-stage custom repair that involved the inclusion of Stellite bar nose inserts.
We successfully restored the blades to a condition that was as good as new. This was done at a fraction of the cost and cycle that would have been required in procuring and installing replacement blades.
Where in-situ blade repair is not an option
There are times when in-situ blade repair is not possible. But that doesn’t mean we can’t restore your blades.
Here are some circumstances in which we can repair blades by removing them from the rotor first:
- Weld repair of titanium blades
- Where midspan damping is too close to the repair area
- Covers with assembly interference
Reduce your outage cycles and costs with EthosEnergy
Our enhanced steam turbine blade repair solutions significantly reduce erosion damage and can extend the periods between your outages. They are also much faster and cheaper – typically 50–60% less costly – than replacement blades.
Compared with manufacturing new blades, our specialist repairs are a sustainable method for reducing your carbon footprint and extending the life of your asset.
Why not find out more? Speak to one of our experts.
Learn more about our steam turbine services
-
Steam Turbines
Increase reliability and efficiency on your steam turbines. Industry-leading engineered solutions and turnkey support for both planned and unplanned maintenance.
-
The smart way to upgrade your existing A10/D11 steam turbines
We are the only service provider offering a complete package of customized solutions for your GE A10 and D11 steam turbines. Whatever the issue, we have the answer.