Reduced outage and costs on a D-11 steam turbine
Patented leading edge restoration process on L-0 titanium blades for a D-11 steam turbine for a large utility company in the southeast US.
- Goals
-
- Reduce Maintenance Spend
- Reduce Forced Outage Rate
- Increase Steam Production
- Life Extension
- Sectors
-
- Power generation
- Asset
-
- Steam Turbines
- Location
- Southeast, USA
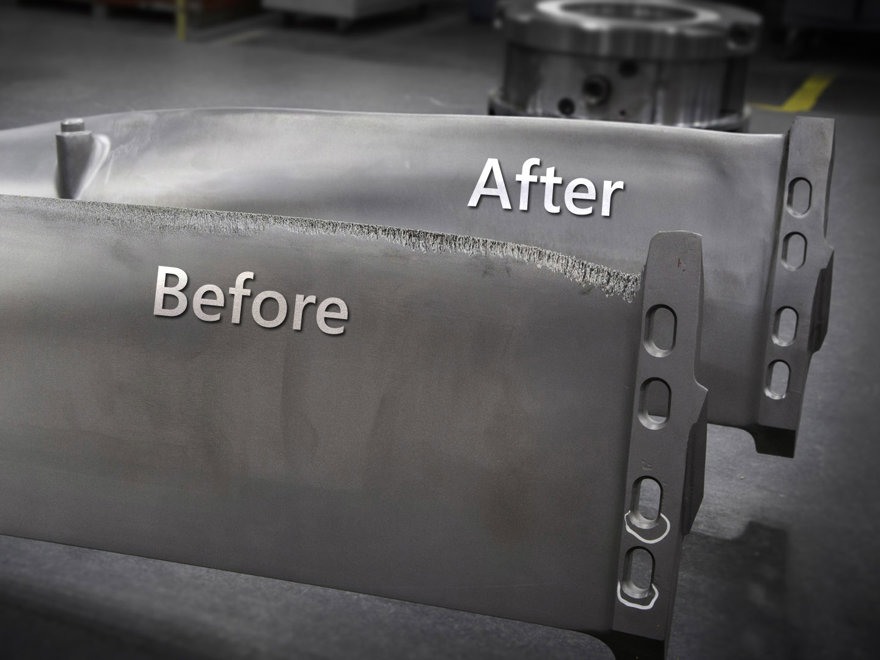
WATCH: Real results on D11 steam turbine
Watch our case study in action
Project Overview
EthosEnergy completed a blade replacement using a patented titanium blade refurbishment process on the L-0 blades of a GE D-11 steam turbine rotor (double flow LP, 300 MW) for a 500+ MW combined cycle power plant.
The work was completed within a 27-day outage timeframe, 9 days ahead of schedule, and the use of EthosEnergy’s refurbishment process reduced costs by over 60% compared to replacement with new blades, restoring the blades to their original aerodynamic profile.
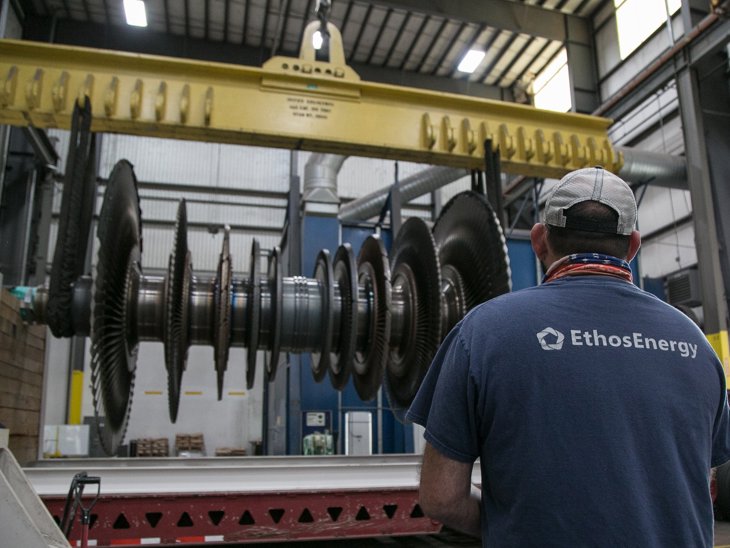
The Challenge
The wet steam environment in the last stages of a D-11 condensing steam turbine, combined with very high tip speeds on long, last stage blades, leads to erosion damage at the leading edge of low-pressure (LP) blading. This erosion can lead to cracks in the blades which in turn causes the blades to fail resulting in catastrophic failure during operation.
Like many other D-11 operators, the customer faced the challenge of the high costs of new blade replacement and long lead times (18-20 months in most cases) from the OEM. Such a long lead time requires more careful planning and timing of blade replacement can be difficult to estimate.
The EthosEnergy Solution
EthosEnergy’s titanium blade refurbishment provided the customer with a cost-effective solution that reduced lead time by over 60%, restoring the blades to their original aerodynamic profile. This extended the life of the blades and improved operation of the unit.
After having completed the refurbishment process on another job previously, EthosEnergy’s blading and production teams were able to reduce the contractual outage timeframe from 36 to 27 days due to improvements in the pin drilling and reaming installation process. The team was also able to arrange permitted freight to expedite the shipment of the rotor back to site three days earlier than the client’s freight provider could secure permits for.
In addition to the leading-edge restoration, the scope of work also included fixing the root of the buckets and correcting loose L-1 blades that were discovered upon inspection in the shop.
About Our Titanium Blade Refurbishment Process
The wet steam environment in the last stages of a condensing steam turbine (including D-11 and A-10 steam turbines), combined with very high tip speeds on long, last stage blades, leads to erosion damage at the leading edge of low-pressure (LP) blading.
Our expert team of skilled engineers and craftsmen have developed an innovative process that restores the 40-inch titanium blade by machining the eroded area, and either welding a titanium insert or weld building with titanium, depending on the extent of the erosion damage.
A full inspection was completed after the process to ensure the integrity of the repair.