Major oil & gas producer puts its trust in EthosEnergy
Seeing the difference with a seawater pump repair
- Goals
-
- Increase Power Output
- Reduce Maintenance Spend
- Sectors
-
- Oil & Gas
- Asset
-
- Supporting Services
- Location
- Qatar, Middle East
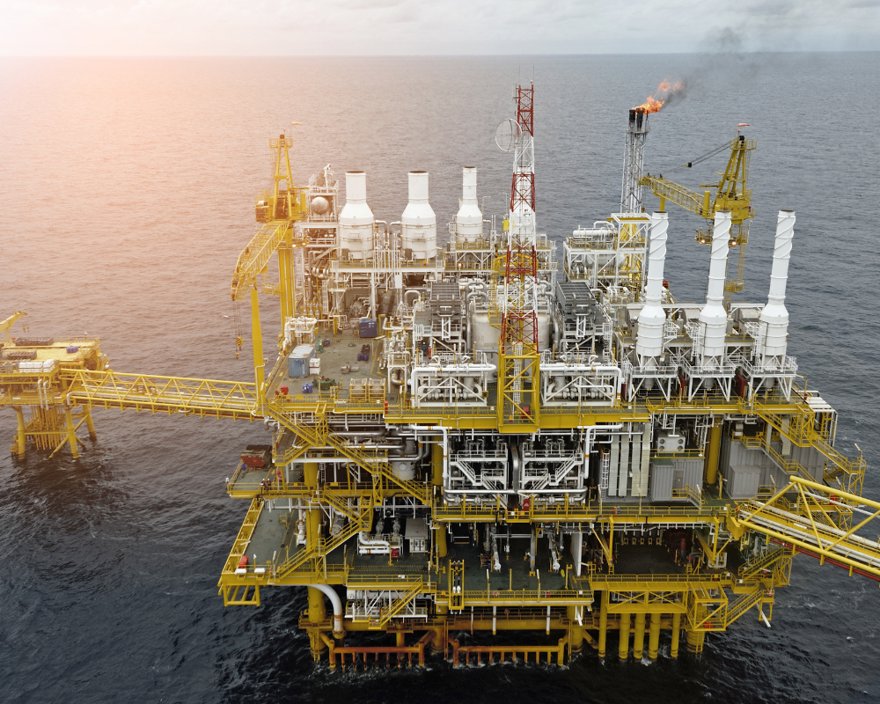
Customer Challenge
A major oil & gas producer in Qatar needed help with repair of a sea pump for its offshore platform. This pump – around 18 to 20 meters in length – was suffering from vibration issues.
The client removed the pump for overhaul. Upon dismantling, they found extensive damage to internal parts.
The impeller was worn out circumferentially. All the Monel alloy shafts and their cutlass rubber bearings were damaged. The aluminium bronze spiders were damaged, and the suction bell and discharge casing were badly worn out. They would need to be replaced … before the standby pump also went down.
The client, however, did not have any spare parts.
The EthosEnergy Solution
One of the client’s employees recommended us. Years before, we had resolved a problem for them. That had left a lasting impression. We examined the pump, put together a scope of work, and provided the client with a quotation. Not only did we come in at a quarter of the OEM’s price but we were able to carry out the work within six months. By contrast, the OEM had a lead time of two years.
Another of our customers gave the client a glowing review of our services, so we won the job. Nevertheless, throughout the project, the client’s quality team scrutinized our work in minute detail. They wanted a paper trail of everything we did – down to the last screw. We passed with flying colors, providing an extensive report with the project delivery. As the work was done locally at our facility in Qatar, the customer could view each stage of the repair and manufacture – an opportunity it took advantage of on an almost daily basis. A third-party surveyor also approved our work.
We inspected and certified the pump columns by checking their alignment and pressure testing them. We were able to salvage some of the parts, such as the spiders. We also saved the impeller by dressing it up, carrying out a slight machining modification, and balancing it. The shafts and bowls, however, were beyond repair so we manufactured new ones. We also gave the client a root-cause solution: We changed the design of the bearing. This enabled it to run dry for a longer period without causing damage
Customer Benefits
The client was extremely happy with our work and impressed by the quality report accompanying it. They said they had never seen such detail or volume of paperwork.
This was a project founded on complete transparency, with fully traceable components and the client being able to inspect our work as often as they wished. We not only demonstrated our expertise in manufacturing parts and extending the life of units but showed we’re a partner that works hard to secure trust. Always.
Key Results
- We almost doubled the life of the pump and its components – the unit was as good as new
- With our much shorter lead time, we reduced the risk of a total outage through the standby pump going down before the main pump repairs had been completed
- Coming in at a quarter of the OEM’s price and lead time, we helped the client save money
- And by minimizing the amount of casting work, we helped reduce carbon emissions
Lifecycle
Lifecycle of the pump and components doubled
Emissions
Carbon emissions reduced through minimizing the amount of casting work
6 months
Lead time of six months compared to the OEM’s lead time of two years
Download our case study here
Looking for more?
We have a wide portfolio of case studies with proven results in the oil and gas industry. View our hand picked examples to read how our maintenance services can help reduce maintenance spend.