Geothermal steam turbine retrofit
Due to the continued steam decline of the geothermal reservoir, the single operating turbine at Tiwi Geothermal Plant (TGP) operated at approximately half capacity and resulted in inefficient steam consumption.
- Goals
-
- Increase Steam Production
- Life Extension
- Increase Power Output
- Sectors
-
- Power generation
- Asset
-
- Steam Turbines
- Location
- Tiwi, Philippines
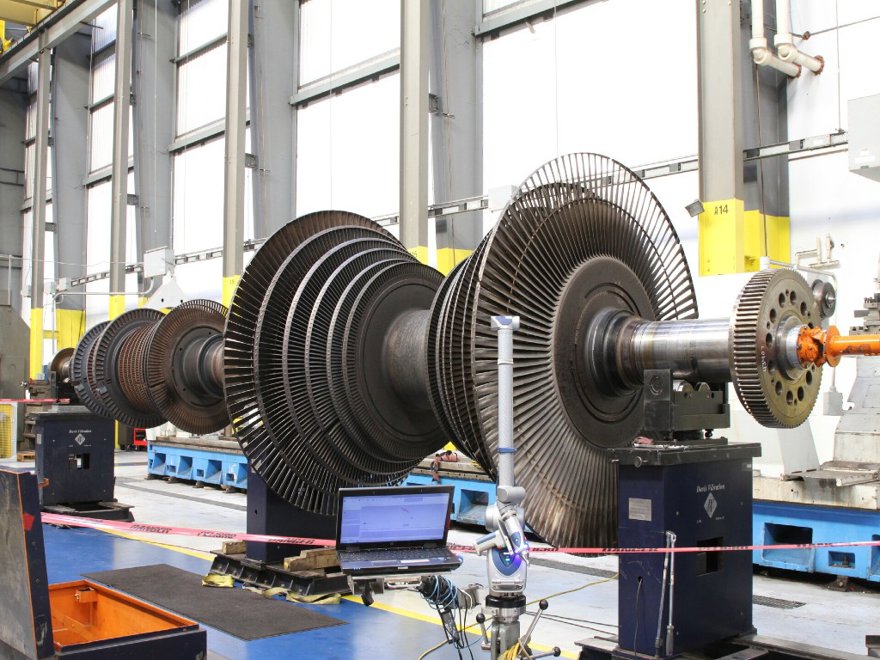
Project Overview
Due to the continued steam decline of the geothermal reservoir, the single operating turbine at Tiwi Geothermal Plant (TGP) operated at approximately half capacity and resulted in inefficient steam consumption.
Key Challenges
- Operator faced with a decreased amount of flow from the geothermal resource
- The turbine which was designed for 60MW was producing less than 30 MW
- The operator was also faced with a steam path which was deteriorated
- Customer keen to minimize cost by using as much of the components that were fit for service as possible
- Unexpected discoveries such as discrepancies in the design of various units caused complications in both the steam path as well as stationary components
The EthosEnergy Solution
EthosEnergy performed a thermodynamic and mechanical analysis of the existing unit and assessed what improvements could be made. From this analysis the turbine diaphragms and blades for three of the six stages were redesigned by reducing the blade height. Since new blades and diaphragms were required, EthosEnergy changed the design to an integral covered configuration with replaceable tip spill strips in the diaphragm. This change eliminated one of the biggest issues on geothermal steam turbine blades which is tenon erosion. The integral cover design eliminates the tenon and allows for improved sealing.
The analysis indicated that six stages were still the best design but the nozzle mouth heights had to be reduced on stages 4 & 5. Even though the steam specific volume went up, the flow required to make the target output of 32.2 MW was lower than the original design volume flow. Nozzle and blade flow passing areas were also changed to account for the change in total volume flow and to distribute the loading optimally across each stage.
Project Highlights
Key highlights of the project
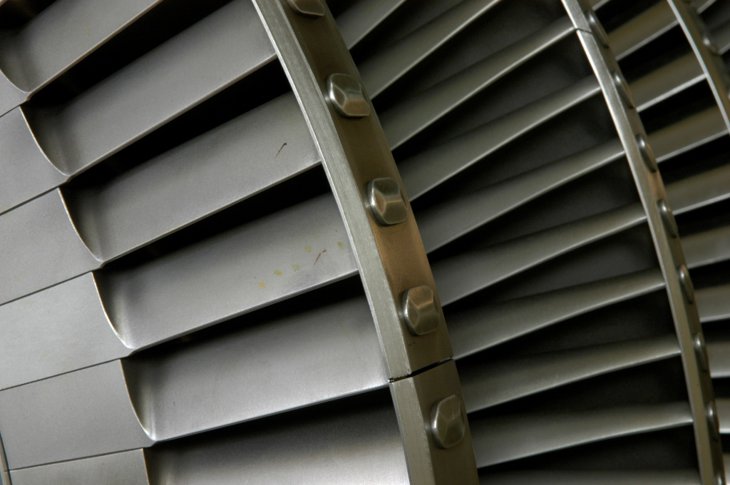
Collaboration between EthosEnergy and Aboitiz Power
Ensured the most cost-effective results by minimizing costs and using as many of the existing components that were fit for service.
Redesign and Modifications
A method of redesign and modifications assured that test results exceeded performance guarantees.
Key Results
The test results exceeded the performance guarantees. The result was a mix of new components for stages 1, 2 & 3 and modifications to stages 4 & 5 to reach a balance between cost and performance gains.
The new steam path was analyzed for the new conditions and material selected to provide improved reliability. The asset now has an extended life due to the well thought out program and execution.
Looking for more?
We have a wide portfolio of case studies with proven results in our steam turbine services. View our hand picked examples to read how we can help.
Find out more
-
Steam Turbines
Increase reliability and efficiency on your steam turbines. Industry-leading engineered solutions and turnkey support for both planned and unplanned maintenance.
-
Upgrades
Whether your process has changed or is undergoing a life cycle extension project, EthosEnergy can redesign your unit to run more efficiently and more reliably, providing optimal performance for years to come.