GS Power Bucheon retrofit project
GS Power engaged KEPCO KPS and EthosEnergy to address the issues of rotor life, steam path degradation and steam path optimization for its latest operating conditions.
- Goals
-
- Increase Steam Production
- Life Extension
- Sectors
-
- Power generation
- Asset
-
- Steam Turbines
- Location
- Bucheon, South Korea
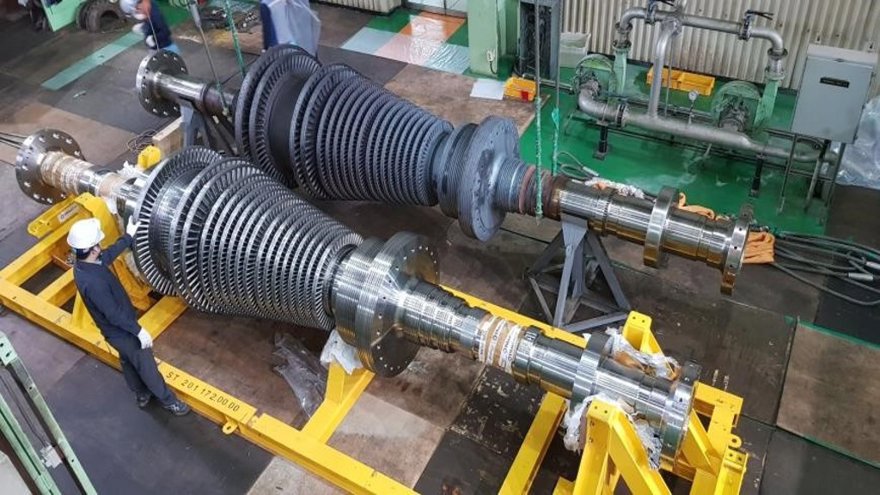
Project Overview
The GS Power installation in Bucheon, South Korea is a Combined Heat and Power (CHP) plant designed to operate in both a “Maximum Power Generation” mode (Mode III) and a “District Heating” mode (Mode I). However, with newer and more efficient combined cycle power plants now supplying the grid, and other economic factors, the Bucheon facility found itself only running at Maximum Power about 10% of the time, and operating primarily in Mode I.
The plant’s operation had also changed, as additional steam was needed for gas turbine NOx control. This now meant that less High Pressure (HP) steam was available at the steam turbine inlet.
Besides off normal operation, the steam turbine (ST) had experienced a reduction in output in all modes, as the steam path had deteriorated. In addition, metallurgical analysis indicated that the HP rotor was approaching the end of its useful life. GS Power engaged KEPCO KPS and EthosEnergy to address the issues of rotor life, steam path degradation and steam path optimization for its latest operating conditions.
Key Challenges
- GS Power required a performance guarantee for the work to be completed. Therefore the challenge was to define the conditions for the new guarantee point.
- Due to the large diameter of the balance piston, wear can lead to a great deal of steam leakage, which equates to a loss in efficiency however EthosEnergy utilized retractable packing to help alleviate this packing wear
The EthosEnergy Solution
The entire section of the steam path needed replaced, however, this blading configuration had always been reliable. Therefore, the decision was made, for stages 1 through 16, to make a “replacement in-kind”, or a replacement of the existing hardware with new, reverse engineered components including the blade carriers and all the interstage seals.
To further improve efficiency, the packing used to seal the balance piston incorporated a brush seal. Brush seals are much more effective than conventional labyrinth seals at reducing leakage. A further benefit of retractable brush seals is the improved seal degradation over time due to the compliance of the bristles.
KEPCO KPS metallurgical analysis identified the need to replace the rotor and a new rotor forging was to be designed, sourced, machined, and assembled by EthosEnergy. New blade carriers and new balance piston packing housings were also supplied.
Project Highlights
The most significant element of the upgrade was the redesign of the original staging between the extraction to the HP heater and the exhaust of the HP turbine. EthosEnergy engineers examined several options, and concluded that a single impulse stage would be more efficient than the two existing reaction stages.
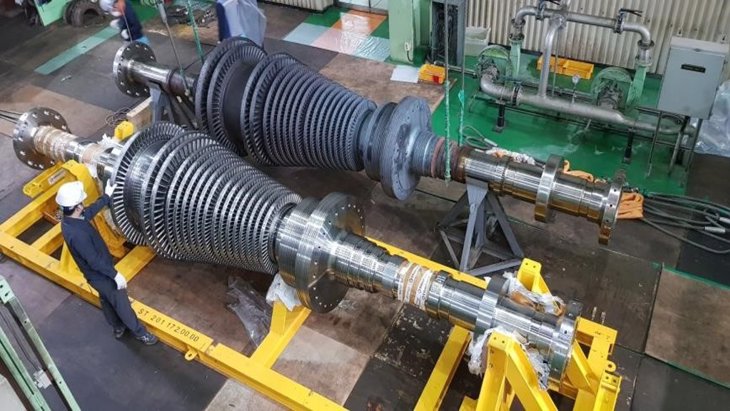
12%
By selecting EthosEnergy’s Engineered
Solution, GS Power extended its steam
turbine’s life by numerous years, increased the plant output at its new design condition by approximately 12%.
State-of-the-art
Utilized state-of-the-art sealing methods that shoul help the unit remain reliable and efficient for years to come.
Ahead of schedule
All parts produced by EthosEnergy were delivered on time and the steam path replacement installation wa completed ahead of schedule. The unit was able to
start up and produce power on the first re-start.
Key Results
This Engineered Solution provided increased exhaust annulus area, higher efficiency, with improved reliability as compared to a simple replacement in-kind.
The test results in the table below shows that the “As Tested” gains were substantially better than the guaranteed values. There are several reasons for this, one is the assumed balance piston leakage before the retrofit to retractable brush seals was very conservative. The gain in Mode I for the improved seal accounted for about half the gains. The assumptions for damage to the tip seals in the HP turbine and steam path degradation was also on the conservative side. KEPCO KPS made other improvements which accounted for 2% of the gains in Mode I.
Find out more
-
SMART Seals®
Customized advanced seals to increase turbine efficiency and availability, lower emissions and maximize your investment
-
Steam Turbines
Increase reliability and efficiency on your steam turbines. Industry-leading engineered solutions and turnkey support for both planned and unplanned maintenance.