Sugar refinery is sweet on our steam turbine services
Rapid response on a steam turbine forced outage saves months on repair lead time for a major sugar refiner
- Goals
-
- Reduce Forced Outage Rate
- Increase reliability
- Reduce Downtime
- Sectors
-
- Power generation
- Asset
-
- Steam Turbines
- Generators
- Field Services
- Location
- Northern California, US
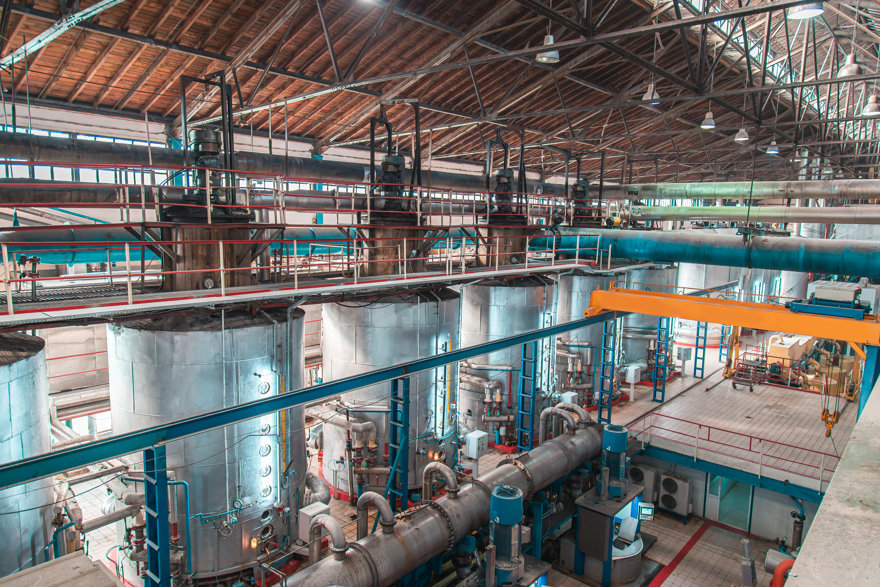
Fast response to a forced outage
One of the world’s largest refiners and marketers of cane sugar, producing around 6 million metric tons of sugar each year, owns and operates numerous sugar refineries across North America and also in Europe.
One of these refineries, based in Northern California, processes over 700,000 tons of cane sugar each year – that’s enough sugar to go in more than 35 billion cans of soda or 152 billion donuts. To do so, the sugar refinery relies on two 5 MW steam turbines to power their operation. These are mature Westinghouse units, commissioned around 1957.
Before 2023, while we had worked at other facilities in the parent company’s portfolio, we hadn’t undertaken any work at this particular site. But we had partnered with a nearby power generation facility. In early 2023, the power plant gave the sugar refinery a reference for us.
Within two weeks, we received an enquiry. One of the sugar refinery’s two steam turbines had gone into a forced outage. Every day it was down, the sugar refinery was losing money and losing the capacity to produce sugar. Could we help?
A candy-do attitude keeps repairs short and sweet
Our project manager received a call on a Friday afternoon briefing him on the situation. By the Monday morning, we had a contract in place for a forced outage and had arrived on site ready to start diagnosing.
The client suspected a grounded generator stator had caused the failure. On inspection, we discovered it was in fact the rotor that was grounded, although the stator was in poor shape. One of the windings had lost its insulation and shorted to the body component.
From the outset, we knew we would have to manufacture two rows of steam turbine blades. But since refurbishing the generator and getting it back online necessitated a longer lead time, our scope of work evolved to include a steam turbine major and stator rewind. It also included work on numerous ancillary items such as the oil pumps, pressure relief valves, and the control valve actuators.
As is the case with many forced outages, we discovered additional issues that had to be addressed. Our client also requested an operating speed balance. When we did that, we found the journal bearings had been plated incorrectly during someone else’s previous repair.
One of the benefits for the client in partnering with us, however, was that – unlike other providers – we didn’t have to farm out work to third parties. We were able to do everything in-house.
Many different EthosEnergy facilities and teams were involved in getting the unit back up and running:
- Our steam turbine repair facility in Perris, California, replaced two rows of buckets on the rotor. They also grit blasted, inspected, and repaired all the steam turbine diaphragms
- Our steam turbine component manufacturing and repair facility in Chicopee, Massachusetts, manufactured all the steam packing and blading that were used by the Perris workshop.
- Our generator services facility in Farmington, New Mexico, performed the rewind of the generator field. They also sent personnel to perform the on-site fieldwork for the generator stator.
- Our EthosEnergy Houston Service Shop performed the operating speed balance as well as the weld repair of the journal bearings on the steam turbine rotor.
- Our Union Field Services out of Northern California, performed all the disassembly and reassembly of the equipment on site, while our field service center in Santa Fe Springs, California, performed all the ancillary component overhauls.
- We also called on our colleagues at Gas Turbine Efficiency (GTE). They came over from Orlando, Florida to inspect and test instrumentation.
On-site, in-house, and back online
The OEM had proposed removing the whole generator to repair it off site. That would have been a monumental task, costing in the region of millions of dollars. But we were able to repair the stator in situ at a fraction of the cost.
Also, because of our in-house capabilities, we helped shorten lead times by a considerable margin. While the steam turbine was out of service, the client was paying a sweet $35,000 a day in rental and fuel costs for the auxiliary equipment it needed to run the facility. So being able to cut lead times by a few months made an enormous difference.
Just as we were commissioning the first unit, the second unit went into a forced outage. But because of budgeting constraints, the client didn’t want us, at this stage, to repeat everything we had done on the first unit. So we focused on getting the turbine back online. We inspected and tested the generator, rewound the field, and reassembled the unit.
Off the back of this successful project execution, EthosEnergy was chosen to carry out the full scope of work on unit two in the future - both the steam turbine and generator stator.
Related content
-
Steam Turbines
Increase reliability and efficiency on your steam turbines. Industry-leading engineered solutions and turnkey support for both planned and unplanned maintenance.
-
Generators
In practice, there is no aspect of a generator repair that we cannot implement: from rewind to upgrade, from repair to overhaul. Clients rely on EthosEnergy to support them with both repair emergencies as well as ongoing maintenance when it comes to industrial generators.
-
Fast resolution for a 10 MW steam turbine forced outage
All systems go for major repairs in the Caribbean
-
Peaking power plant restored to peak performance
Generator forced outage case study. From beginning to end, the work took us just 45 days. This was as much as 10 days quicker than you would normally expect for turnaround on a project of this nature – especially during an outage season in the US.