Gas turbine leaking flange repair
A repair after inspection revealed that flames had burned through the blank flange which controls the flow of air, to purge the nozzle tip on these gas only units.
- Goals
-
- Increase Power Output
- Decrease Heat Rate
- Life Extension
- Sectors
-
- Power generation
- Asset
-
- Heavy Gas Turbines
- Location
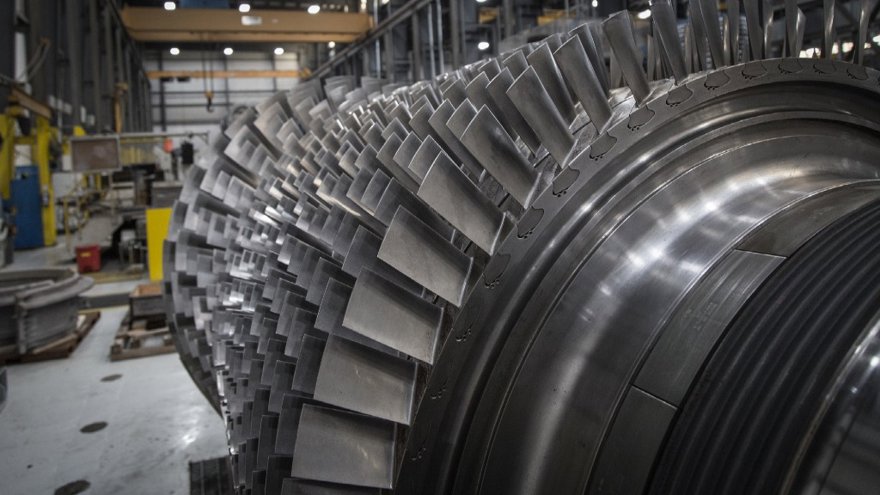
Project Overview
Thirty minutes after starting up a Frame 7FA+e, the gas turbine enclosure temperature had reached 300°F. Half an hour later, when the temperature had reached 350°F, an operator went to the enclosure to investigate. Upon opening the enclosure door the operator saw flames coming out of one of the end covers. The unit had been tripped and an investigation was initiated. The initial inspection revealed the flames had burned through the blank flange, which controls the flow of air, to purge the nozzle tip on these gas only units.
Key Challenges
A large enough leak at the blank flange could cause hot gas at the nozzle tip to flow back into the endcover where it will ultimately cause a complete failure. This failure cascade was consistent with the observed nozzle and end cover damage.
The EthosEnergy Solution
- Check the fit-up of the end caps on the unit. The triangular blank flanges can be difficult to install without cocking. Proper torque-up sequence & torque settings should be followed
- When removing the blank flange, use a flat-face lifting tool. A pointed tool, such as a scribe, is almost certain to make an indentation that could allow air to leak
- Check the origin of the seal rings. The OEM has previously used two suppliers for this part with the part numbers being the same, but not equal in configuration. One of the seal rings is jacketed with a material that tends to deteriorate above 500°F even though the temperature in this region is roughly 600°F
- Check the length of the cap screws. There may be a mixture of the 1.25” & 1.5” fasteners. The 1.25” screws are too short to engage the helicoil locking feature & should not be used
- EthosEnergy installs a more suitable seal as part of our overhaul services. This hardware is also available to customers as a replacement kit
Project Highlights
The key highlights of the project.
Seals
Seals employed by the OEM are manufactured with a thick cladding that can oxidize heavily and break down at typical operating temperatures
Bolts
Bolts used to secure the blank flange to the end cover can be too shorts to fully engage the helicoil locking feature and can lead to an air leak
500°F
One of the seal rings is jacketed with a material that tends to deteriorate above 500°F even though the temperature in this region is roughly 600°F
Key Results
The leak at the blank flange was caused by a seal failure. Bolts used to secure the blank flange to the end cover can be too short to fully engage the helicoil locking feature in these holes, leading to an air leak at the blank flange & initiating the failure observed
Blank cartridges are commonly removed from borescope units between combustion inspections. Special care should be taken to use new seals &properly torque bolts to the recommended levels.
Find out more
-
Parts & Component Repairs
We provide comprehensive replacement and spare parts solutions that meet or exceed OEM performance, including hot gas path parts, combustion components, and fuel nozzles
-
Heavy Gas Turbines
The largest independent provider of heavy gas turbine repair and maintenance services – with specialised expertise in GE frame units, including 7F, and OEM capabilities for Fiat Avio and mature Westinghouse turbines.